Actiw автоматизировал производственный склад CCEN для
максимального использования существующего склада с высокой пропускной способностью
Заказчик: Coca-Cola European Partners Norway
Страна: Норвегия
Coca-Cola European Partners Norway (CCEPN) — норвежский производитель безалкогольных напитков и крупнейший в Норвегии завод по розливу напитков Coca-Cola. Ранее предприятие называлось Coca-Cola Enterprises Norway (CCEN) и работало как производственный склад и как пункт прямой доставки товаров в магазины.
The system delivers
100%
inventory control
Бизнес задачи: повышение эффективности и функциональности операций по розливу в бутылки
На территории CCEN находился огромный обычный малоэтажный склад, состоящий из зданий разной высоты. Хранение продукции осуществлялось в основном методом блочного штабелирования. Из-за нехватки складских мощностей на своем предприятии CCEN арендовала складские помещения за его пределами, что привело к дополнительным расходам на транспортировку и размещение продукции. Поэтому существующие складские операции нуждались в значительной модернизации, чтобы соответствовать будущим целям CCEN по повышению эффективности, гибкости и производительности операций по розливу. Компания хотела иметь большую гибкость в отношении будущих новинок продукции и разнообразия упаковки, потенциальных изменений в бизнесе, роста объема основных единиц складского хранения (SKU) и снизить затраты на переполнение склада.
CCEN рассматривала этот проект как возможность дальнейшего повышения безопасности, сокращения воздействия человеческого фактора и вмешательств в работу, а также как путь к значительному повышению точности инвентаризации и эффективности отгрузки.
Вместе с тем, крайне важно было, чтобы любая модернизация склада не оказала негативного влияния на текущую деятельность компании CCEN и ее клиентов.
Задача:
- высокая пропускная способность;
- высокая плотность хранения продукции;
- малоэтажные имеющиеся здания;
- динамическая корректировка и эксплуатационная гибкость для учета изменений пропускной способности и производительности.
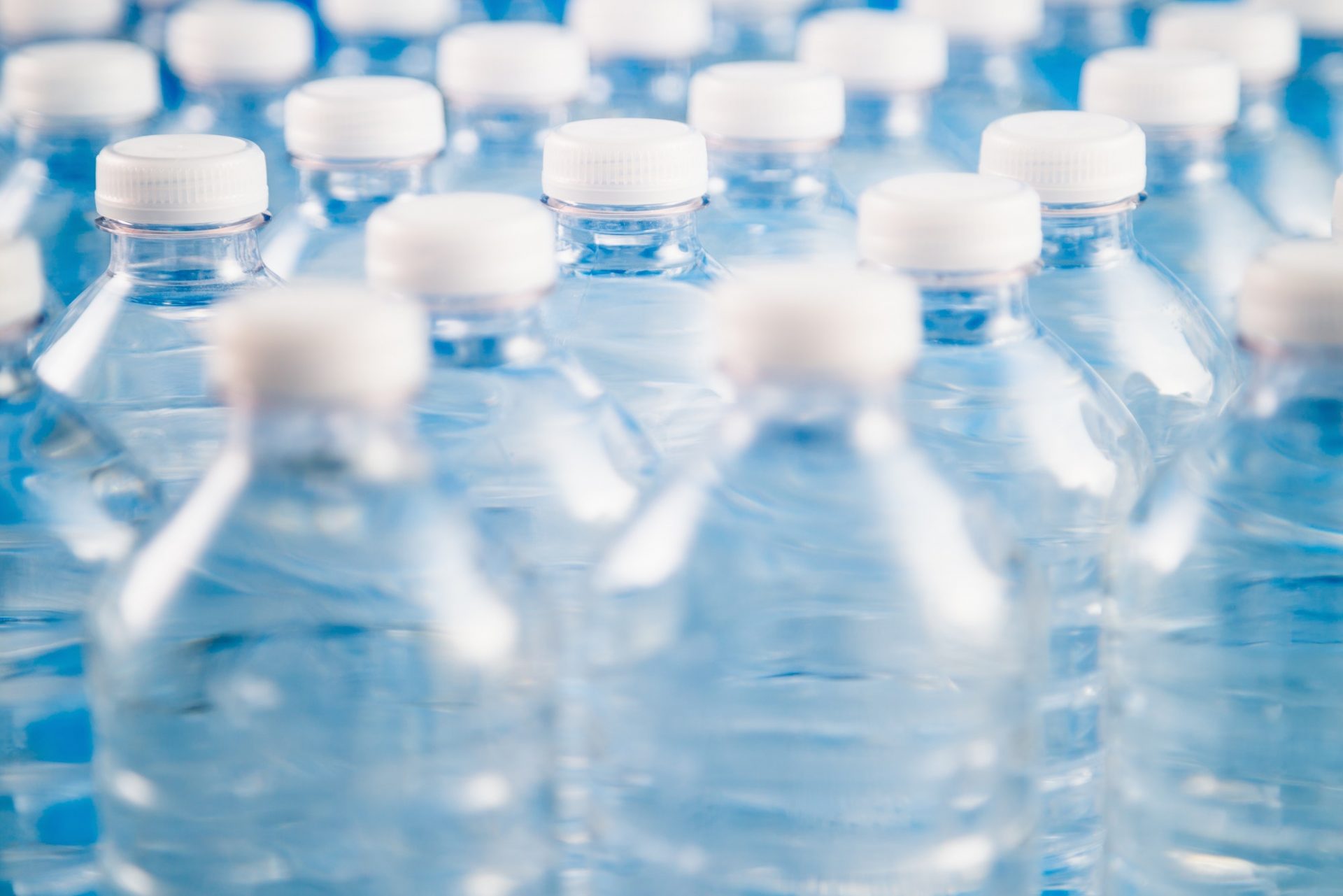
Решение: уникальная автоматизированная система хранения и отгрузки с возможностью размещения 21 000 нетто-позиций для поддонов
После анализа имеющихся технологий компания CCEN остановила свой выбор на уникальной технологии динамического хранилища Actiw. Решение Actiw по высокой плотности хранения смогло обеспечить 21 000 нетто-позиций для поддонов без каких-либо изменений в существующем малоэтажном складском помещении. Система имеет высокую пропускную способность — 760 перемещений поддонов в час (вход — максимум 430 поддонов/ч, выход — максимум 330 поддонов/ч), работая при загрузке в 94 % доступных позиций поддонов.
Специалисты Actiw установили двухмодульную систему, которая позволяет складировать, сортировать и укладывать грузы на поддоны в точной последовательности. Отгрузка осуществляется на 20 двухдорожечных наклонных конвейерах (что соответствует 20 заказам), при этом водители грузовиков выполняют загрузку с помощью паллетных тележек с электроприводом.
Система Actiw была разделена на два отдельных блока, что способствовало поэтапной установке и вводу в эксплуатацию, при этом система для обеспечения высокой плотности хранения была введена в эксплуатацию первой, чтобы освободить место для второй установки. Это позволило клиенту продолжать выполнять текущие работы во время установки, а также обеспечило высокую гибкость во время нормальной эксплуатации.
Для упрощения конвейерной системы потоки поддонов с производственных линий и сторонних бутилировочных компаний (предприятий по розливу продукции по индивидуальному заказу) были сгруппированы в три зоны подачи на склад. Поддоны идентифицируются, проверяется их форма и наклон перед передачей на одну из точек входа Actiw. Одобренные поддоны продолжают движение в систему Actiw. Непригодные грузы направляются на отбраковочный узел для доработки и возврата в систему.
Алгоритмы хранения системы Actiw направляют вертикальные подъемники, транспортеры поперечного перемещения и транспортеры с углубленными полосами на позиционирование поступающих поддонов в системе в зависимости от времени их получения. Это гарантирует, что следующие поддоны, которые стоят в очереди на выход, уже на пути выхода из транспортера с углубленными полосами или приближаются к нему для быстрого доступа.
Результаты: более эффективное и рентабельное хранение и отгрузка
В результате склад стал значительно более эффективным, экономически выгодным и экологически чистым. Были достигнуты цели по увеличению объема хранения и транспортировки, а необходимость в использовании складов сторонних компаний отпала. Система была полностью введена в эксплуатацию в течение 14 месяцев, то есть с опережением графика. Благодаря тому, что каждый поддон укладывается отдельно и без использования вилочного погрузчика, проблемы с повреждением продукции, которые ранее возникали при блочном штабелировании и использовании ручного труда, были устранены.
Необходимость проведения ручных манипуляций между производственными линиями, зоной комплектации и доком была сведена к минимуму, что позволило снизить затраты на логистические операции. Благодаря такой складской гибкости клиент может с большей эффективностью использовать будущие возможности или потенциальные изменения в своем ассортименте продукции.
Кроме того, новая система позволяет контролировать складские запасы на 100 % Несмотря на высокий уровень автоматизации, обслуживание системы остается безопасным и простым, поскольку обычные периодические проверки и обслуживание происходят в основном вне конструкции стойки.